Working group leader:
Christian Polley M.Sc.
Justus-von-Liebig Weg 6
18059 Rostock
Tel.: +49 381 / 498 - 9113
Fax: +49 381 / 498 - 9092
Email: christian.polley(at)uni-rostock.de
Room: UT17
Additive manufacturing - material development
Additive manufacturing enables the production of components from pure polymers, metals or ceramics. Different additive manufacturing processes are used depending on the requirements of the component and material. Each process requires a specially prepared material, which is either ordered or produced in-house. For example, powder bed-based 3D printers require a powder with a defined particle shape and particle size distribution. Additive manufacturing processes based on the photopolymerization principle require a photopolymer with a specific viscosity and defined curing kinetics over time with low scattering. It can be seen that, depending on the process, various material parameters must be adapted to the process in order to obtain a print product that is as accurate and stable as possible.
The chair of microfluidics develops its own material systems for various 3D printers. A wide range of processing and analysis equipment is available to staff and students for this purpose. If powders are to be ground and analyzed, the ball mill can be used to reduce the particle size and the particle analyzer can be used to determine the particle shape and size. The rotational rheometer and the UV module can be used to analyse and develop photopolymerizing liquids and suspensions. Glass rotation plates are available for this purpose, which are illuminated from below by a light source with a defined wavelength and intensity, thus stimulating the photopolymer to react. The reaction kinetics are recorded with the aid of an oscillating movement of the two rotation plates.
Current research projects
Piezoelectric materials for multifunctional bone and cartilage implants
The investigations in this sub-project (B01) of the SFB Elaine focus on the production of electrically active implants for bone and cartilage regeneration using additive manufacturing technology. The implants for bone replacement are manufactured using special processes for the various applications. For the load-bearing area, e.g. hip endoprostheses, implants made of a biocompatible titanium alloy are intended, which carry specific structures for improved mechanical behavior and bone ingrowth. In addition, the implants are coated with a novel conductive polymer with incorporated Bioglass© particles in order to increase the electrical activity at the implant-bone interface. Implants made of barium titanate and Bioglass© are being developed for the non-load-bearing area. These are intended to promote natural bone growth by utilizing the piezoelectric effect and thus improve the ingrowth of the implants. For cartilage regeneration, novel hydrogel scaffolds incorporated with electrically conductive polymer are additively manufactured and seeded with cells. This process step is carried out by the close cooperation partner, the Chair of Biomaterials at the Friedrich-Alexander University Erlangen-Nuremberg. In addition, the working group from Erlangen brings considerable expertise in handling Bioglass© particles to the project. The scaffolds produced in B01 form the basis for the work of other working groups within the ELAINE research network.
Person in Charge:Phillip Barkow, M.Sc
Project duration: 07/2017 - 12/2025
Please note: Once you watch the video, data will be transmitted to Youtube/Google. For more information, see Google Privacy.
Funded by:
in cooperation with:
Universität Rostock: IEF, MSF, UMR
EMAU Greifswald
Universität Leipzig
Universität Nürnberg-Erlangen
Leibniz-Institut für Plasmaforschung und Techologie e.V.
Electrical and mechanical stimulation of cartilage

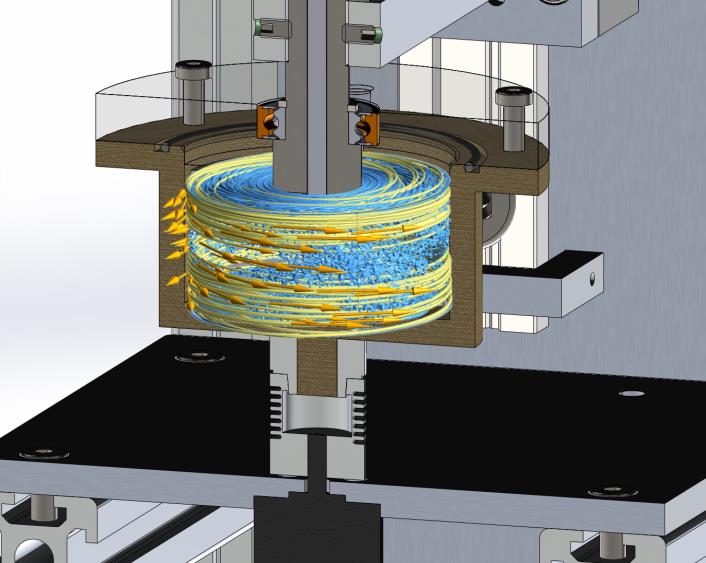
The aim of the subproject (C02) of the SFB Elaine is to analyze the influence of electrical and mechanical stimulation on the chondrogenic differentiation of human cartilage cells and mesenchymal stem cells. This sub-project is being carried out in collaboration with the Research Laboratory for Biomechanics and Implant Technology at Rostock University Medical Center. The scaffolds developed in subproject B01 will be used as a scaffold for the cultivation of cartilage cells. A 3D stimulation chamber is being developed specifically for the experimental investigations, which makes it possible to apply electrical or mechanical stimulation or even a combination of both types of stimulation. Key issues include determining the configuration of the electrodes and implementing the mechanical actuators for shear and pressure loading of the cells. In addition, a protocol for electrical and mechanical stimulation is being developed that leads to optimized proliferation and differentiation of the cartilage cells and mesenchymal stem cells. In addition, a comprehensive "multiphysics" simulation model is to be created that maps the stimulation processes (electrical and mechanical) and the effect on the cells (e.g. shear stress) and contributes to a better understanding of the mechanical and bioelectromagnetic stimulation processes.
The long-term aim is to optimize the ex vivo 3D cultivation of cartilage cells and mesenchymal stem cells by means of electrical and mechanical stimulation in the context of autologous cartilage cell implantation using a collagen- and hydrogel-based 3D implant (scaffolds).
Person in charge:Nada Abroug M.Sc.
Project duration: 07/2017 - 12/2025
Please note: Once you watch the video, data will be transmitted to Youtube/Google. For more information, see Google Privacy.
Partners:
Universität Rostock: IEF, MSF, UMR
EMAU Greifswald
Universität Leipzig
Universität Nürnberg-Erlangen
Leibniz-Institut für Plasmaforschung und Techologie e.V.
Completed research projects
RESPONSE: 3D printing of functionalized (bio)materials
In the research network "RESPONSE - Partnership for Innovation in Implant Technology", the Chair of Microfluidics is working on the development of individualized implants for ear, nose and throat medicine* as well as on the process and material development of functionalized (smart) (bio)materials for the different 3D printing technologies Composite Extrusion Modeling (CEM) and Digital Light Processing (DLP). In the case of the CEM process, the processing of biodegradable metal matrix composites (BMMC) is to be investigated. In collaboration with the Chair of Materials Engineering at the University of Rostock, the focus is on the material properties resulting from the interaction of metallic and polymeric materials, such as an adjustment of the degradation properties or the degree of crystallinity of the polymer. In the application of the DLP process, the focus is on particle-loaded and stimuliresponsive polymers. For example, it is being investigated how the electrostimulative behavior of photopolymers, e.g. piezoelectric properties, can be influenced by the introduction of ceramic particles (Figures 1 and 2). Furthermore, it is planned to process thermoresponsive materials in the process in which thermal stimulation is suitable for influencing the release of active ingredients.
Funded by: Federal Ministry of Education and Research (BMBF) as part of the "Twenty20 - Partnership for Innovation" program
Person in charge: Dipl.-Ing. Robert Mau
Partners: RESPONSE – Partnerschaft für Innovation in der Implantattechnologie
The aim of the research project is to develop drug delivery systems (DDS) with time-controlled drug release. These should enable the implant-based, local administration of active ingredients and combinations of active ingredients with specific predetermined release mechanisms. A new 3D printing process is required to manufacture these DDS, which will be based on a combination of microstereolithography and inkjet technology. This process will be used to produce the basic body of an implant via stereolithographic cross-linking and the active ingredient will be loaded via inkjet modules in the same process. The resulting drug depots enable controlled and predictable drug release, as properties such as the drug concentration can be adjusted during the process.
The project is being carried out in collaboration with the Institute of Biomedical Engineering at the University of Rostock.
Person in charge: M.Sc. Jan Konasch
Project duration: 01.09.2017 - 31.08.2019